Wo wird in der Industrie am meisten Energie verbraucht?
Das energieintensivste Anwendungsfeld in der Industrie ist die Prozesswärme (siehe Grafik). Hier wird gut zwei Drittel der gesamten Endenergie im industriellen Sektor verbraucht. Elektrische Antriebe und davon angetriebene Aggregate wie Pumpen, Motoren, Ventilatoren und Kompressoren folgen beim Energieverbrauch an zweiter Stelle. In industriellen Betrieben mit mehr als 20 Mitarbeitern benötigen sie 22 Prozent der eingesetzten Energie. Neun Prozent der Endenergie wird zum Heizen genutzt, gut zwei Prozent fallen für die Beleuchtung an. Dann folgen mit je einem Prozent die Verbrauchsbereiche Klimakälte, Warmwasser und Informations- und Kommunikationstechnik (IKT).
Endenergieverbrauch nach Anwendungsbereichen 2014
Wo liegen die größten Einsparpotenziale in der Industrie?
Am meisten Energie können industrielle Betriebe in den Anwendungsbereichen Prozesswärme, mechanische Energie und bei der Erzeugung von Druckluft sparen:
Prozesswärme
Die effizientere Nutzung der Prozesswärme bietet in der Industrie das größte Einsparpotenzial. Fast jeder verarbeitende Betrieb ist auf industrielle Wärme für die Dampf- und Heißwassererzeugung und für den Betrieb von Brennöfen und Trocknungsanlagen angewiesen. Verschiedene Studien zeigen: Unternehmen könnten hier durch energetische Optimierungs- und Modernisierungsmaßnahmen im Schnitt rund 15 Prozent ihrer Energiekosten einsparen. Vor allem schlecht isolierte Industrieöfen, veraltete und nicht an den Bedarf angepasste Anlagen, sowie eine fehlende Abwärmenutzung sind hier große Kostentreiber.
Tipps für eine wirksame Optimierung der Prozesswärme
- Modernisieren Sie Wärme- und Dampferzeugungsanlagen
80 Prozent der industriellen Wärme- und Dampferzeugungsanlagen in Deutschland sind älter als zehn Jahre und entsprechen nicht mehr dem aktuellen Stand der Technik. Durch modernste Technologien könnten hier pro Jahr 9,6 TWh eingespart werden. Dies entspricht zwei Prozent des gesamten Energieverbrauchs für Prozesswärme in Deutschland.
- Minimieren Sie Ihren Wärmebedarf und Ihre -verluste
- Nutzen Sie Maßnahmen zur Wärmerückgewinnung:
zum Beispiel für die Brauch- und Prozesswassererwärmung, Warmwasserbereitung, Vorwärmung von Verbrennungs- und Trocknungsluft oder als Raumwärme.
- Verwenden Sie energieeffiziente Komponenten
Regelbare Brenner, Kessel mit großen Wärmeübertragungsflächen und drehzahlgeregelte Antriebsmotoren für Gebläsebrenner und Pumpen ermöglichen große Einsparungen beim Energieverbrauch.
- Optimieren Sie Regelung und Steuerung
Stimmen Sie Ihre Feuerungsanlagen immer auf den tatsächlichen Bedarf ab. Eine Mehrkesselregelung sorgt beispielsweise dafür, dass nur die wirklich erforderliche Anzahl von Kesseln geschaltet wird.
Elektrische Antriebe und davon angetriebene Aggregate
Motorensysteme wie Elektromotoren, Pumpen, Kompressoren und Ventilatoren bieten bei den Strom-Querschnittstechnologien die größten Einsparpotenziale. Im industriellen Bereich sind sie für rund 70 Prozent des Stromverbrauchs eines Unternehmens verantwortlich. Betrachtet man den gesamten Lebenszyklus eines Motors, liegen die Kosten für den Stromverbrauch bei rund 96 Prozent der Gesamtkosten. Die Anschaffungskosten liegen bei nur 2,5 Prozent.
Tipps für eine wirksame Optimierung elektrischer Antriebe
- Einsatz von Frequenzumrichtern bei variablem Leistungsbedarf
Dies ermöglicht Ihnen Einsparungen zwischen 10 und 50 Prozent.
- Korrekt dimensionierte Antriebe
Das Einsparpotenzial liegt bei 10 Prozent.
- Hocheffiziente Motoren nutzen
Hocheffiziente Motoren (Effizienzniveau IE2) bieten bei hohen Betriebsstunden (> 4.000 h/a) große Einsparmöglichkeiten – abhängig von den Betriebsstunden und der Leistungsklasse.
- Steuerung bedarfsgerecht einrichten
Schalten Sie nicht benötigte Antriebssysteme aus und optimieren Sie die Anlagensteuerung.
- Kraftübertragung verbessern
Bevorzugen Sie immer Direktantriebe, da diese verlustfrei sind. Vermeiden Sie Kraftübertragungen mit Keilriemen. Einsparpotenzial: bis zu 40 Prozent.
Druckluft
Die Erzeugung von Druckluft ist sehr energie- und kostenintensiv: Im Durchschnitt verbraucht sie gut zehn Prozent des Strombedarfs eines Industriebetriebs – und die Einsparpotenziale sind enorm. Oftmals geht gut die Hälfte der eingesetzten Energie auf dem Weg zum Werkzeug verloren. Die Gründe dafür sind ganz unterschiedlich: minderwertige Technik, Leckagen, Verzicht auf günstige Alternativen, Druckverluste, fehlende Kompressorsteuerung, ungenügende Wartungskonzepte und der Verzicht auf die Nutzung der Abwärme.
Tipps für eine wirksame Optimierung
- Verzicht auf Druckluft
Verwenden Sie Druckluft nur für die fertigungstechnisch notwendigen Zwecke und nicht zum Trocknen oder Reinigen. Rüsten Sie so oft wie möglich auf Elektromotoren um, da sie viel weniger Energie als Kompressoren benötigen.
- Wartung und Instandhaltung
- Leckagen suchen und beheben
Undichtigkeiten im Druckluftnetz können Sie mit Ultraschall und Schaumsprühgeräten aufspüren.
- Druckhöhe verringern
Halten Sie den Netzdruck möglichst niedrig. Prüfen Sie, ob beispielsweise eine dezentrale Druckerhöhung möglich ist, wenn nur einzelne Verbraucher hohen Druck benötigen.
- Steuerung und Laufzeiten optimieren
Ermitteln Sie den Ist-Zustand Ihres Druckluftsystems. Ergeben sich Auffälligkeiten, können Sie konkret ansetzen: etwa an der Auslegung der Kompressorgrößen, der Dimensionierung des Druckluftbehälters oder der Wasserkühlung.
- Abwärme nutzen
Nutzen Sie die Abwärme der Kompressoren zum Beispiel für die Gebäudeheizung oder Warmwasserbereitung.
Wo es noch weitere Einsparungen gibt, erfahren Sie in unserem kostenlosen E-Book Energieeffizienz. Darin gehen wir 6 Energiefressern auf die Spur und entdecken für Sie zahlreiche Effizienzmaßnahmen, Fördermöglichkeiten und Praxisbeispiele.
Fazit: Energieeffizienz in der Industrie
Die Liste der Ansatzpunkte ist lang – und genau das führt zu einem Dilemma: Manche Betriebe lassen sich von der Länge der Aufgabenliste gleich abschrecken. Andere versuchen aus eigener Kraft den „großen Wurf“ und scheitern an der schieren Projektgröße oder Re-Priorisierungen im Unternehmen.
In der Praxis hat es sich bewährt, das Vorgehen in Phasen aufzuteilen. Zunächst sollte man gemeinsam mit einem spezialisierten Energieberater den Bedarf analysieren. Das Ergebnis ist eine Prioritätenliste, die zeigt, wo sich Einsparpotenziale besonders kostengünstig realisieren lassen: die „quick wins“. Zeigen sich aus diesen Maßnahmen erste Einsparerfolge, dann lösen sich innerbetriebliche Widerstände meist in Luft auf, und man kann im Effizienzprojekt weitere Maßnahmen in Angriff nehmen.
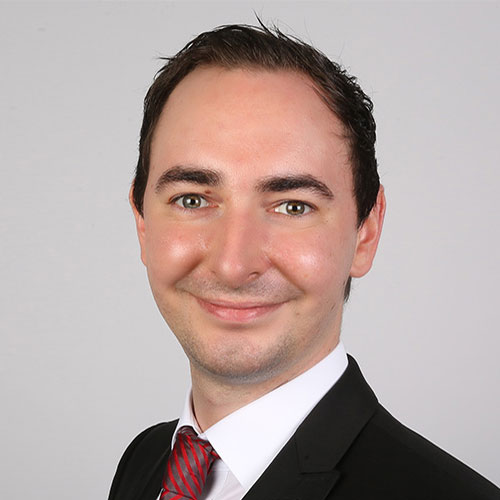
Autor: David Wagenblass
Produktmanager Elektromobilität, MVV Enamic GmbH
David Wagenblass ist seit 2007 in verschiedenen Positionen für MVV tätig. Über 10 Jahre verantwortete er das Kooperationsmanagement im Geschäftskundenvertrieb. Aktuell ist er für die Entwicklung und Vermarktung von Ladeinfrastrukturlösungen für Unternehmen und Wohnimmobilien zuständig.
Inhaltsverzeichnis
- Wärmeversorgung (14)
- Steuern und Abgaben (13)
- Dekarbonisierung (11)
- Energiemessung (10)
- E-Mobility (9)
- Energiemanagement (9)
- Fördermittel und -programme (8)
- Kälte-, Klima- und Lüftungstechnik (8)
- Nachhaltigkeit (7)
- Energiebeschaffung Strom / Gas (6)
- Photovoltaik (6)
- Rechenzentrum (6)
- Beleuchtung (5)
- Druckluft (5)
- Wärmepumpe (5)
- Experten-Interview (4)
- Lastmanagement (4)
- Stromspeicher (4)
- Fernwärme (3)
- Netzentgelte (3)
- Energieaudit (2)
- Power Purchase Agreement (2)
- Wasserstoff (2)
- ISO 50001 (1)